1. DISTRIBUCIÓN DE MERCANCÍA Y MOVIMIENTO DEL AIRE EN LA CÁMARA
Frecuentemente se asocia un tipo de evaporador a cada tipo de cámara. De hecho es habitual que se empleen evaporadores cúbicos para cámaras de refrigerados y congelados, evaporadores tipo mural para los túneles de congelación y enfriamiento rápido, y evaporadores de techo para las salas frías. Si bien esto suele aplicarse de manera general, la elección del evaporador debe pasar por una serie de fases que permitirán una mejor selección del mismo y una optimización del movimiento del aire en el recinto.
Lo primero que debemos tener en cuenta es la distribución de la mercancía en la cámara, cuánto producto se va a almacenar y cuál va a ser la mecánica de funcionamiento del cliente en dicho almacén. Supongamos una cámara de 20 m x 10 m de planta y 4 m de altura, en la cual se van a almacenar 200.000 kg de producto, que deberá mantenerse a 0 ºC y 85 % de humedad relativa, requiriéndose una potencia frigorífica de 60 kW (Figura 1).
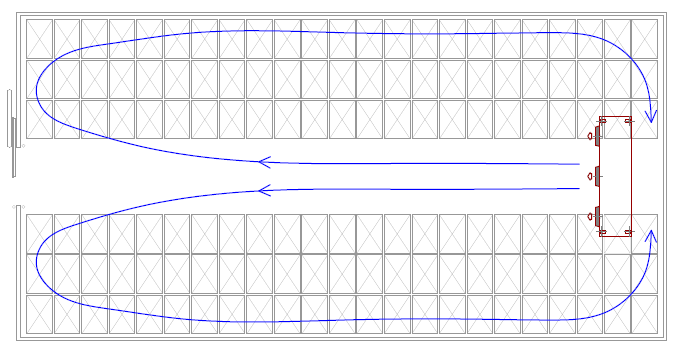
Figura 1. Distribución de la mercancía y circulación de aire en la cámara.
El flujo de aire en la cámara debe ser tal que toda la mercancía sea alcanzada por el aire proyectado por el evaporador. En el almacenamiento en vertical, deberá dejarse libre como mínimo la altura del evaporador, para permitir una buena circulación del aire por la parte superior de la cámara (Figura 2).
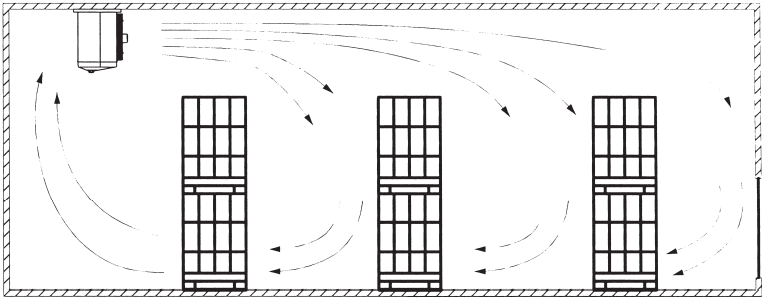
Figura 2. Circulación vertical del aire en la cámara.
Es muy importante verificar que el evaporador tiene “tiro” suficiente para que el aire alcance la longitud total de la cámara, pues de lo contrario el producto más alejado del evaporador no alcanzará la temperatura requerida.
2. SELECCIÓN DEL EVAPORADOR
Para seleccionar adecuadamente el evaporador debemos prestar atención a los siguientes aspectos:
- Refrigerante y compatibilidad con el material del evaporador.
- Tipo de construcción: cúbico, mural, techo…
- Potencia frigorífica requerida.
- Humedad relativa en la cámara y salto térmico refrigerante – aire.
- Separación entre aletas.
- Número y tamaño de los ventiladores.
Los evaporadores para refrigerantes fluorados o CO2, suelen construirse con tubería de cobre y aletas de aluminio. Por otra parte, los evaporadores para amoníaco deben ser de acero inoxidable. Los evaporadores más empleados para los recintos frigoríficos son los de convección forzada, siendo los más empleados los cúbicos, los de techo y los murales (Figura 3).
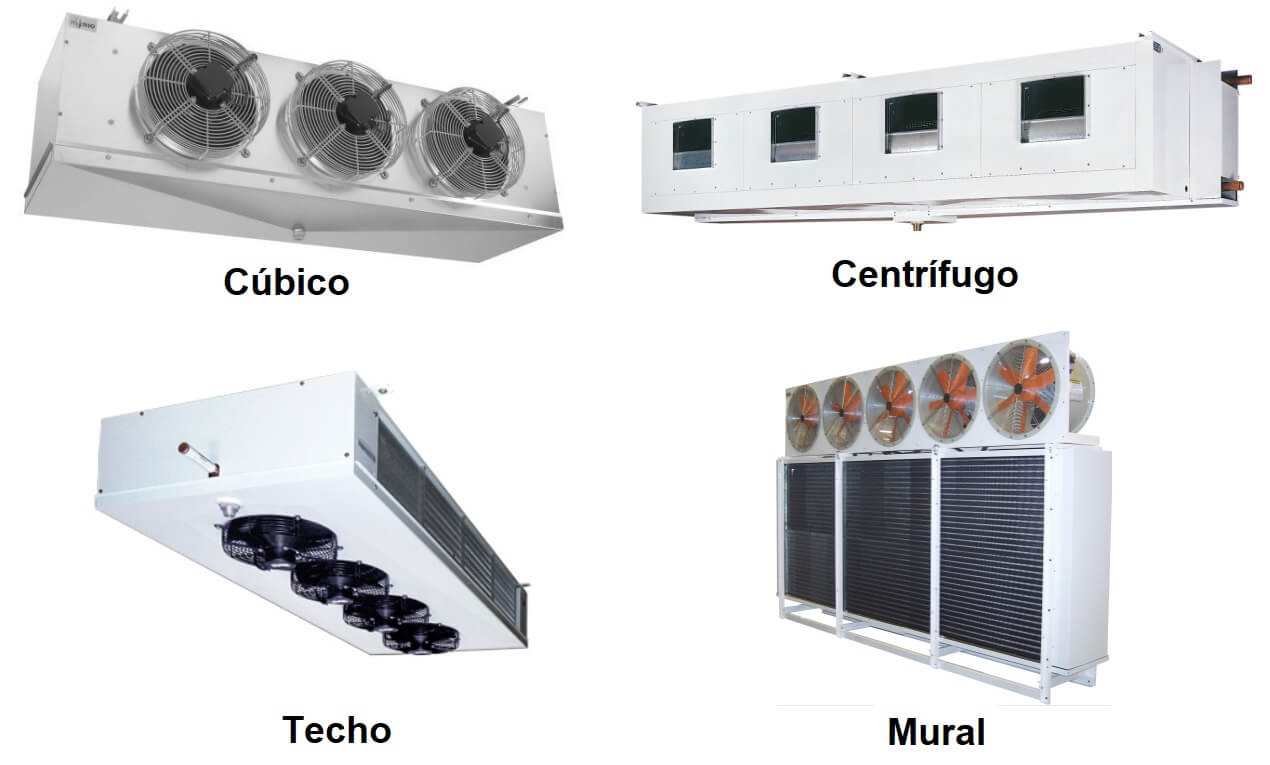
Figura 3. Tipos de evaporadores.
– Evaporadores cúbicos: Son los más usados en cámaras frigoríficas por su sencillez y efectividad.
– Evaporadores de techo: Se emplean en salas refrigeradas donde trabaja personal, ya que realizan una distribución de aire a baja velocidad y lanzado paralelamente al techo para evitar molestas corrientes de aire.
– Evaporadores murales: Utilizados en túneles de congelación y enfriamiento, por su gran potencia de ventilación y su óptima distribución del aire.
Por el interior de los evaporadores circula el refrigerante, y por el exterior el aire ambiental, existiendo un salto térmico de 5 a 10 K entre el refrigerante y el aire entrante, que suele enfriarse entre 3 y 5 K al pasar por el evaporador.
En cuanto a los sistemas de desescarche, este puede ser mediante resistencias eléctricas, por agua, o por gas caliente. En instalaciones industriales de cierto tamaño es frecuente emplear el sistema de desescarche por gas caliente.
Volviendo al caso que nos ocupa, el evaporador más apropiado suele ser por lo general el cúbico, así que elegiremos uno de este tipo. Para ello vamos a emplear el catálogo comercial de Pecomark. Buscamos en la sección de evaporadores cúbicos para refrigerante fluorado y vemos que puede ser adecuada la gama ICE del fabricante ECO (páginas 280 a 285).
Vemos que hay varios modelos que podrían ser adecuados para nuestro proyecto. Ahora debemos fijarnos en un detalle importante, la separación entre aletas (mm). Esto es importante debido a que los evaporadores que trabajan a temperaturas de evaporación por debajo de 0 ºC generan escarcha en el evaporador, y el espacio entre aletas puede verse obstruido por el hielo. Es por ello que los evaporadores deben tener una separación mínima entre aletas dependiendo del tipo de cámara:
- Cámaras y túneles de congelados: Separación de aletas entre 8 y 10 mm.
- Cámaras de refrigerados: Separación de aletas entre 6 y 8 mm.
- Salas frías: Separación de aletas entre 4 y 6 mm.
En nuestro caso, puede ser apropiados los evaporadores cúbicos ICE con separación de aletas 6 mm (páginas 280 y 281).
Ahora vemos que debemos elegir entre evaporadores con ventilador de hélice ɸ 560 o 630 mm. Veremos que hay modelos de ambos tipos que pueden servirnos; la diferencia es que los que tienen ventiladores de menor diámetro requerirán más número de ventiladores para proporcionar el caudal de aire necesario.
Otro factor a tener en cuenta es el salto térmico DT (K) entre el refrigerante y el aire de la cámara que retorna al evaporador. Este DT influirá directamente en la humedad relativa de la cámara, como vimos en este artículo. En nuestro caso la H.R en la cámara debe ser del 85 %, por lo que a través de la gráfica (Figura 4) podemos ver que el DT debe ser de aproximadamente 6 K para el caso de evaporadores ventilados.
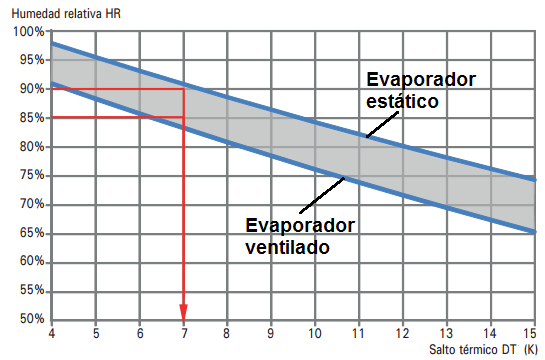
Figura 4. Salto térmico y humedad relativa en la cámara.
Según esto, vemos que existen dos modelos que cumplen con el requisito de 60 kW de potencia frigorífica y DT = 6K. Tenemos el modelo ICE-54 B06 (Figura 5), y el modelo ICE-63 B06 (Figura 6).
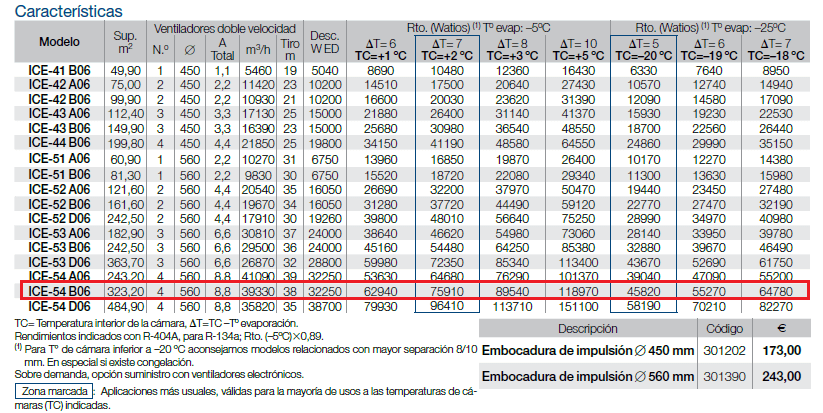
Figura 5. Evaporador ICE-54 B06.
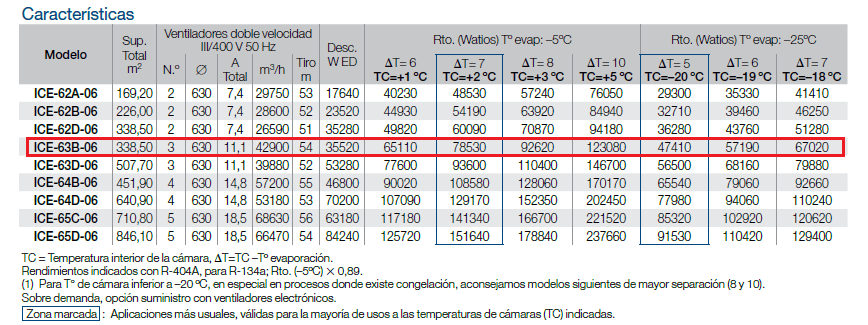
Figura 6. Evaporador ICE-63 B06.
Se puede ver que ambos evaporadores dan la potencia frigorífica con DT = 6K.
El ICE-54 es de 4 ventiladores, 63 kW de potencia, 323,2 m2 de superficie y 39.330 m3/h de caudal de ventilación con tiro de 38 m. Coste PVP 17.874 euros con sistema de desescarche por gas caliente.
El ICE-63 tiene 3 ventiladores, 65 kW de potencia, 338,5 m2 y 42900 m3/h de caudal con tiro de 54 m. Coste PVP 22.180 euros.
Puesto que ambos cumplen con los requisitos, en principio se podría seleccionar el ICE-54, que tiene un consumo eléctrico inferior en los ventiladores y es algo más económico. Sin embargo, este evaporador es más largo (4,85 m) que el de tres ventiladores (3,75 m), por lo que en ciertas ocasiones donde hay un espacio limitado, habría que tener en cuenta las dimensiones de cada evaporador.
3. VÁLVULAS DEL EVAPORADOR
La central frigorífica suministrará refrigerante líquido a los diferentes evaporadores repartidos por la industria. Cada evaporador dispondrá de la valvulería básica (2 y 3), y en el caso de que el desescarche sea por gas caliente, requerirá de valvulería adicional (4 a 10) (Figura 7). Todas las válvulas se suelen montar en el techo de las cámaras frigoríficas formando el conocido “piano o estación de válvulas”.
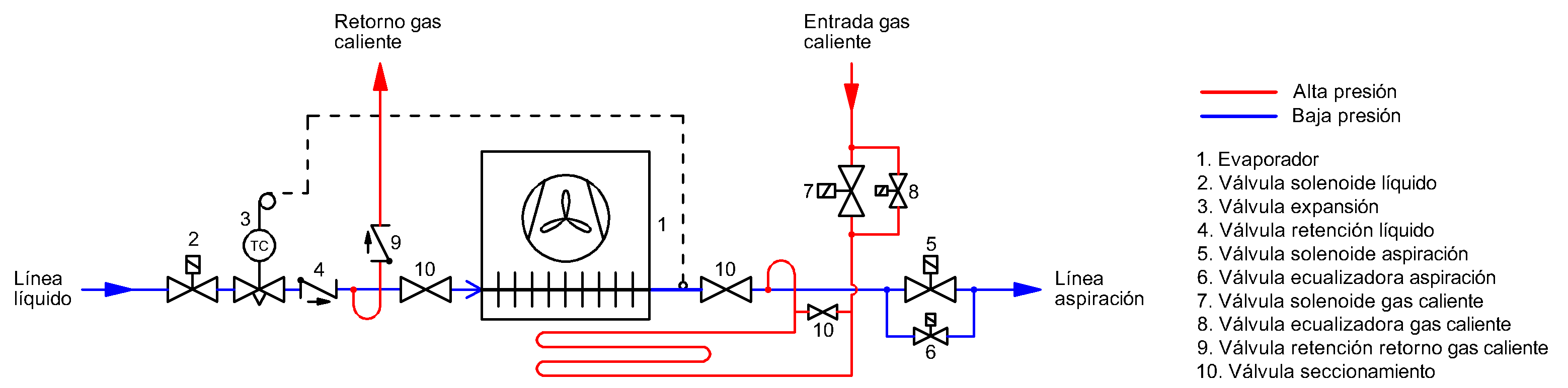
Figura 7: Esquema frigorífico de valvulería para evaporador.
La secuencia de funcionamiento del desescarche por gas caliente es se puede ver en este anterior artículo.